Le soudage dans l’EN 1090-2 – Partie 5: les contrôles non destructifs
Cette dernière partie de la série des publications Métalétech – Le soudage dans l’EN 1090-2 aborde les contrôles exigés au niveau des soudures finies. Il est important de noter que même si la NF ISO 14731 (voir article Métalétech Le soudage dans l’EN 1090-2 – Partie 2) fait également référence aux contrôles avant et pendant le soudage, la NF EN 1090-2 (notée EN 1090-2 dans la suite) précise uniquement des exigences pour le contrôle après soudage.
Contrôles
L’EN 1090-2 introduit trois types de contrôles avec des objectifs distincts :
- Essai de type dont l’objectif est d’évaluer un mode opératoire nouvellement introduit dans la fabrication ;
- Essai de base (essai de routine) dont l’objectif est d’assurer la qualité en fabrication continue ;
- Essai propre au projet (essai spécifique) dont l’objectif est de contrôler des assemblages spécifiques, afin d’assurer la qualité des soudures dans des assemblages fortement sollicités et/ou des soudures d’une importance élevée pour la résistance de la structure globale.
Essai de type
Après la qualification d’un nouveau mode opératoire de soudage, il convient de vérifier si les paramètres validés à travers la qualification de mode opératoire de soudage (QMOS) sont également valables en condition de fabrication. Ainsi, on doit contrôler les 5 premiers assemblages réalisés selon une nouvelle QMOS. La longueur minimale cumulée à contrôler est de 900 mm. Pour valider l’essai type, le niveau de qualité B selon la NF EN ISO 5817 (notée ISO 5817 dans la suite) est exigé indépendamment de la classe d’exécution visée.
Essai de base
Après avoir confirmé la validité d’une QMOS à la suite de l’essai type, des contrôles de routine doivent être réalisés en fabrication. Il convient de noter que toutes les soudures doivent être contrôlées visuellement sur toute leur longueur indépendamment de la classe d’exécution visée. Si un défaut en surface est détecté lors du contrôle visuel, un essai par ressuage ou magnétoscopie est à effectuer obligatoirement.
Outre le contrôle visuel, l’EN 1090-2 demande la réalisation d’essais non destructifs supplémentaires dont le pourcentage dépend de la classe d’exécution comme montré au Tableau 1. Pour la classe d’exécution EXC1, dans l’EN 1090-2 il est estimé que le niveau de qualité des soudures peut être assuré grâce à l’aptitude démontrée des soudeurs qualifiés. Il n’est alors généralement pas nécessaire d’effectuer des essais non destructifs (END) supplémentaires.
On peut noter que la méthode d’essai END supplémentaire n’est pas imposée dans l’EN 1090-2. Il est recommandé de se référer à la norme NF EN ISO 17635 pour choisir une méthode d’essai adaptée au problème traité (voir publication Métalétech : Essais non destructifs des soudures). En particulier, on peut noter qu’il est très difficile d’effectuer des essais volumétriques pour les cordons d’angle et les soudures par pénétration partielle. Pour ces soudures, on doit privilégier les essais de surface (essais par ressuage ou magnétoscopie).
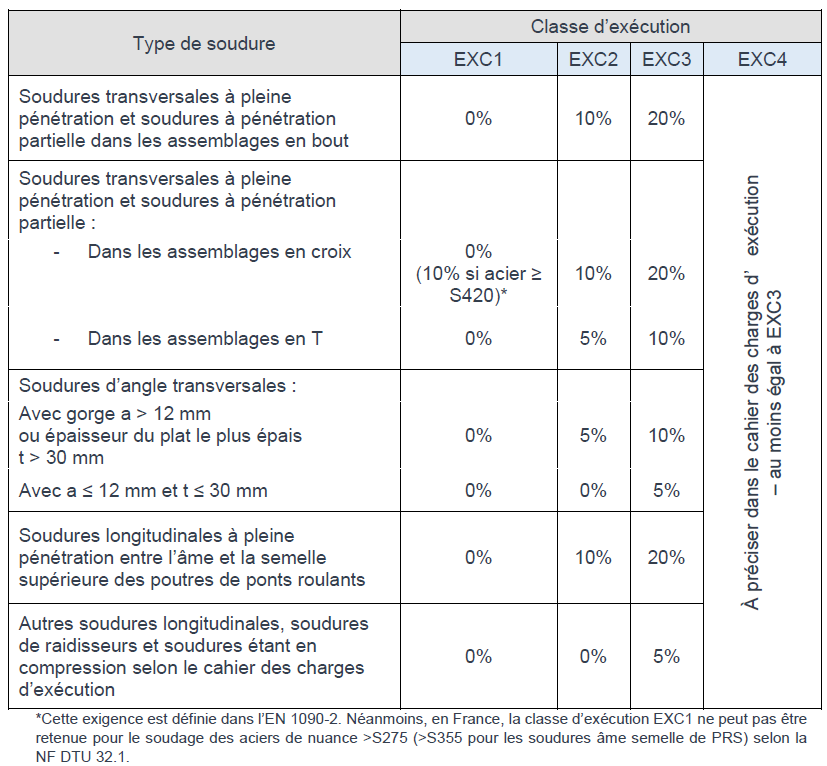
Les pourcentages donnés au Tableau 1 doivent être répartis sur l’ensemble de la fabrication en couvrant autant que possible l’ensemble des soudeurs, l’ensemble des postes de soudage, l’ensemble des DMOS, etc. En fonction de la longueur des soudures individuelles, le contrôle doit être réalisé de la manière suivante :
- Par défaut, chaque soudure d’une longueur minimale de 900 mm doit être contrôlée sur une longueur égale à p% de la longueur totale (p étant le pourcentage indiqué au Tableau 1) ;
- Si toutes les soudures ont une longueur inférieure à 900 mm, il convient de contrôler autant de soudures que nécessaire pour atteindre p% de la longueur cumulée de l’ensemble des soudures dans le lot (un lot de soudures peut correspondre à toutes les soudures du même type, par exemple : soudures réalisées entre platines et traverses pour un bâtiment industriel) ;
- Si la longueur cumulée de toutes les soudures d’un lot de contrôle est inférieure à 900 mm, au moins une soudure doit être contrôlée sur sa longueur totale (si avec cette longueur on n’atteint pas p% de la longueur totale, il convient de continuer le contrôle avec une deuxième soudure).
Finalement, en fonction de la classe d’exécution, le niveau de qualité de la soudure doit être conforme au niveau « D », « C » ou « B » défini dans l’ISO 5817 (voir Tableau 2). Pour la classe d’exécution EXC4, le niveau doit être précisé dans le cahier des charges d’exécution.
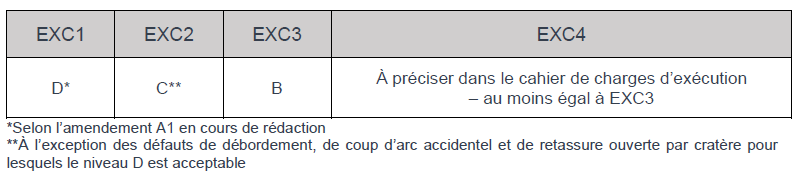
Essai propre au projet
En classe d’exécution EXC1, EXC2 et EXC3, il est possible de définir des assemblages soudés spécifiques dans le cahier des charges d’exécution pour lesquels des essais non destructifs doivent être réalisés. Par exemple, cela peut être le cas pour les assemblages ayant une géométrie inhabituelle pour le fabricant.
Pour la classe d’exécution EXC4, le cahier des charges d’exécution doit identifier les essais propres au projet, c’est-à-dire les assemblages et l’étendue des essais (au minimum égale à l’EXC3 – voir Tableau 1).
Traitement des non-conformités
En cas de détection de non-conformités, il convient de réaliser des essais complémentaires selon le schéma suivant qui est basé sur les informations de l’Annexe C de la version 2010 de la NF EN ISO 17635 (ISO 17635 par la suite). Cette Annexe a été supprimée dans la version actuelle de l’ISO 17635 mais les informations seront introduites dans l’EN 1090-2.
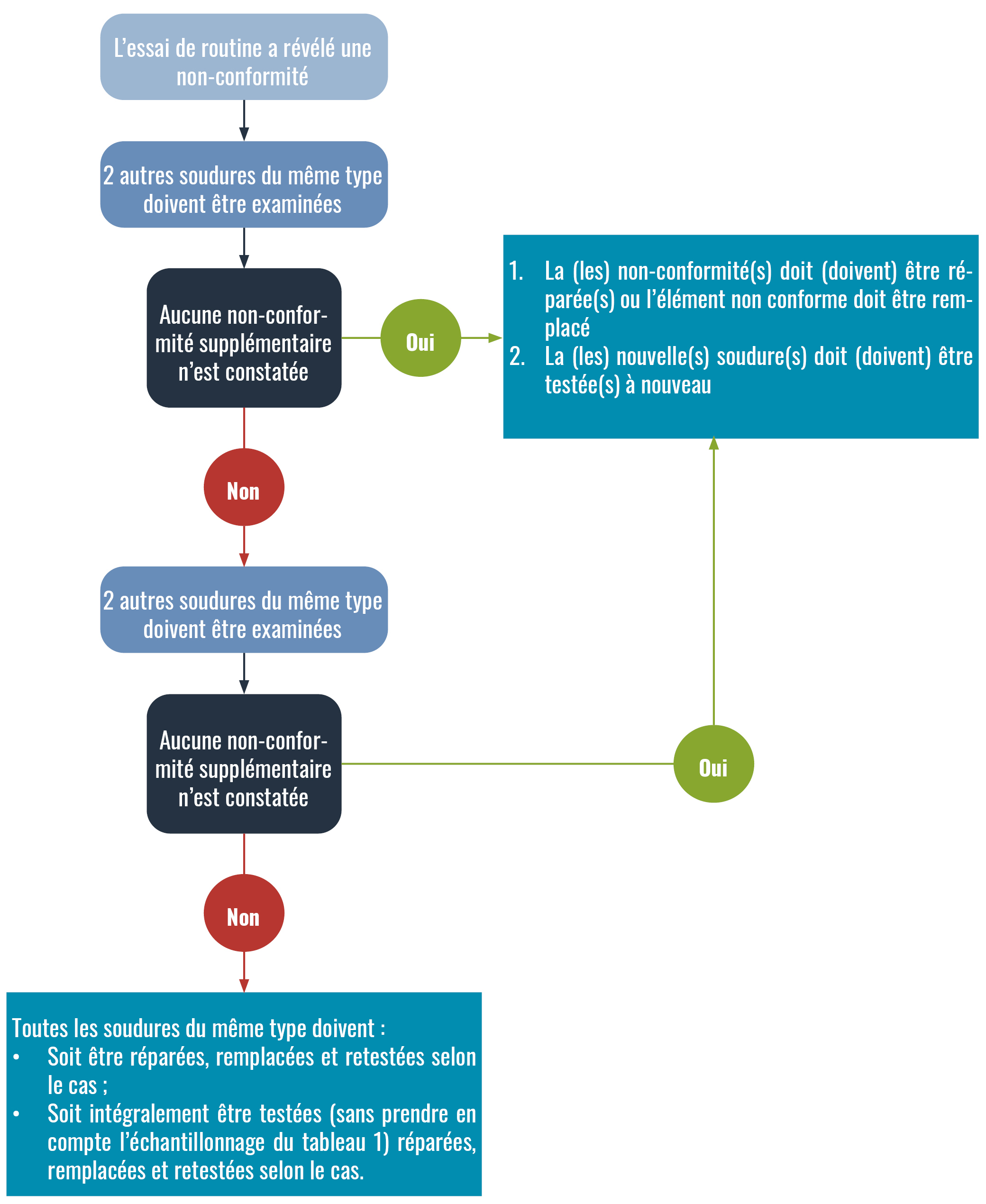
Qui a le droit de réaliser les contrôles non destructifs ?
L’EN 1090-2 n’exige pas de compétences particulières pour la réalisation d’examens visuels. Néanmoins, les personnes réalisant ce type de contrôle doivent avoir un minimum de connaissances vis-à-vis des défauts éventuels et des critères d’acceptation.
En revanche, les contrôles non destructifs de type ultrason, ressuage ou magnétoscopie doivent être réalisés par une personne qualifiée au niveau COFREND 1. Le rapport interprétant les résultats doit être signé par une personne qualifiée au niveau COFREND 2. Les contrôleurs peuvent faire partie de l’entreprise car l’EN 1090-2 n’exige pas un contrôle réalisé par une tierce partie indépendante. Cependant, la réalisation des essais non destructifs est, dans nombreux cas, sous-traité à des organismes extérieurs.
André Beyer, directeur de projet recherche – CTICM