Joints de rails de pont roulant
Les rails de pont roulant constituent des éléments essentiels du chemin de roulement. Selon les spécifications du projet, ces rails peuvent être soit des profilés laminés simples soudés à la semelle supérieure de la poutre de roulement, soit des rails à large patin conçus spécifiquement à cet effet (voir fiche précédente).
En fonction du type de rail sélectionné, plusieurs options sont envisageables quant à leur installation : la réalisation de joints de fabrication à chaque travée de poutre de roulement ou la pose continue sur toute la longueur de la voie de roulement.
Rail continu ou discontinu
Dans le cas des rails soudés à la semelle supérieure de la poutre de roulement, il est recommandé d’interrompre le rail à chaque extrémité des poutres de roulement, qu’il s’agisse d’un joint de construction ou d’un joint de dilatation du bâtiment. Cette disposition est nécessaire pour éviter un bridage excessif susceptible de générer des contraintes importantes dans le rail et ses soudures.
Certains types de rail spécifiques, tel que les rails à large patin (Burbach) sont installés avec des dispositifs de fixation indépendants autorisant les déformations longitudinales du rail. Il n’est pas nécessaire d’interrompre ces rails à chaque extrémité des poutres de roulement. La continuité entre deux tronçons de rails consécutifs est alors généralement réalisée par soudure.

Joints de rails discontinus
Les joints de rails doivent être conçus de manière à réduire au minimum les chocs qui peuvent endommager les galets. Une coupe en biseau d’un angle de 45° ou en escalier au niveau des joints de dilatation du bâtiment, voir Figure 1, décalée de l’extrémité des poutres de roulement, est obligatoire. Le décalage recommandé du joint par rapport à l’extrémité de la poutre de roulement est d’environ 300 mm.
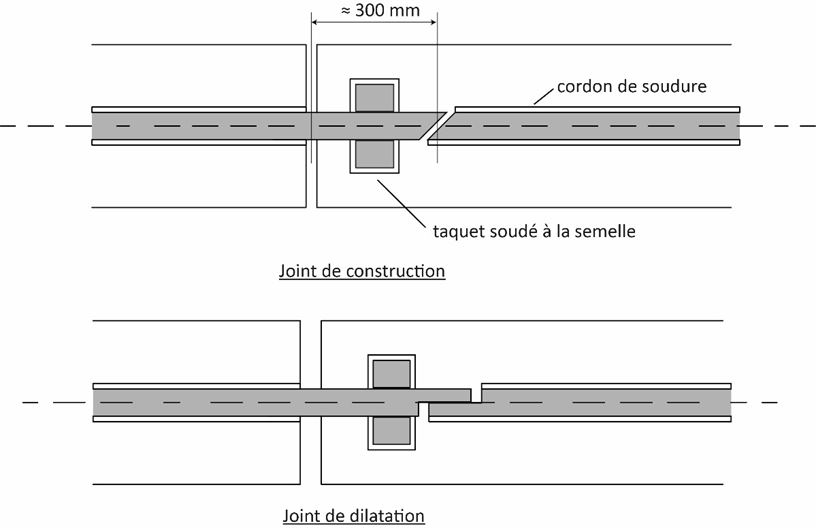
Lorsque les rails sont discontinus, la transmission des efforts horizontaux pour la partie du rail qui se trouve au-delà du joint de poutre, doit être garantie. Des taquets peuvent être soudés de part et d’autre du rail, afin de reprendre les efforts transversaux sans brider les déformations longitudinales.
Joints de rails continus
Dans le cas des rails continus, l’analyse de la structure supportant l’appareil de levage doit prendre en compte les impacts potentiels de cette continuité, notamment vis-à-vis des effets de la dilatation ou du retrait thermique, le cas échéant, et des efforts d’accélération et de freinage du pont roulant.
Ils doivent être positionnés à une distance minimale de L/10 par rapport à l’appui de la poutre de roulement, mais jamais à moins de 500 mm de celui-ci, où L représente la portée de la poutre de roulement. Cette distance peut être réduite à L/20 en présence d’un appuis élastomère.
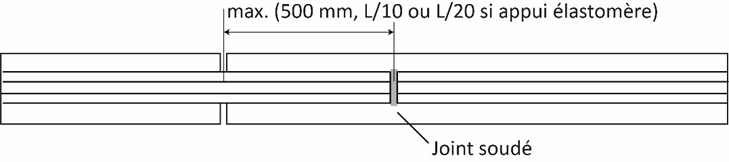
Tolérances de pose
Il existe deux normes traitant des tolérances de poses des poutres de roulement la NF EN 1090-2 [1] avec et l’ISO 12488-1 [2] . Il convient de rappeler que la première est la norme d’exécution des ouvrages de charpente métallique, tandis que la seconde concerne les engins de levage.
Cas des rails discontinus
Dans le tableau B.9 de la NF EN 1090-2 [1] , le détail 4 spécifie l’écart de niveau admissible entre deux rails consécutifs, tandis que le détail 5 présente le décalage limite en plan entre ces mêmes rails, voir Figure 3 . Ces deux détails sont fournis pour n’importe quel type de rail : carrés, rectangulaires ou Burbach. Les valeurs des tolérances associées à ces deux détails dépendent de la classe de tolérance retenue. Par défaut, les critères de la classe 1 doivent être respectés, et seules les spécifications du marché peuvent conduire à l’adoption de la classe 2 (voir NF EN 1090-2 §11.3.2[1] ).
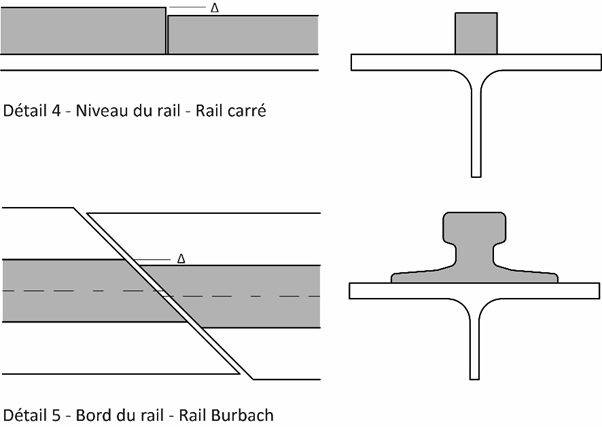

Dans l’ISO 12488-1 [2] , les mêmes détails sont repris avec des niveaux de tolérance identiques. Cependant, il est mentionné qu’en cas de décalage de bord, un meulage avec une pente de 1/50 doit être prévu pour corriger ce décalage.
Bien qu’il n’existe actuellement aucune référence normative concernant l’écart longitudinal entre deux rails consécutifs séparés par un joint, il est néanmoins judicieux de limiter cet espace au maximum afin de réduire les chocs et les vibrations. En dehors des limites imposées par d’éventuels effets de dilatation thermique, un écartement maximal de 2 mm semble approprié et est parfois défini dans certains projets.
Cas des rails continus
De plus, l’ISO 12488-1 [2] ajoute qu’il est nécessaire de contrôler l’inclinaison du rail dans le plan, de part et d’autre d’un joint soudé. Ce critère est pertinent car il limite les poussées au vide qui peuvent se développer lorsque le rail est comprimé ou tendu.
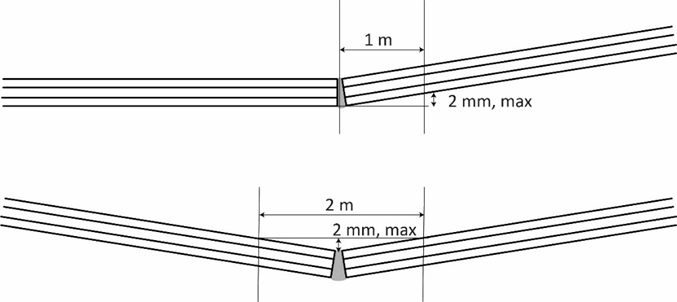
Cas particulier des rails continus par soudure aluminothermique
Pour réduire les chocs dus aux décalages inévitables entre deux rails consécutifs et qui peuvent entraîner, notamment, une usure prématurée des galets, la réalisation de joints de continuité soudés tend à se développer dans le domaine des engins de levage.
Le processus de soudage aluminothermique est déjà largement utilisé dans l’industrie ferroviaire pour assembler les sections de rail en acier de manière efficace et fiable. Il permet de réaliser des soudures in situ sans démonter les voies. Cette technique utilise un alliage métallique en fusion qui, lorsqu’il est appliqué sur les surfaces à assembler, génère une réaction exothermique, formant ainsi une soudure de continuité entre les éléments. Ce processus est utilisé pour réparer les rails endommagés ou pour allonger leur longueur.
Avant le soudage, les extrémités des rails sont coupées à une longueur spécifique pour créer un espace, puis alignées et entourées d’un moule réfractaire pour résister à la chaleur. Les rails sont préchauffés pour libérer les contraintes résiduelles, puis un creuset contenant les composés en poudre est placé au-dessus du moule. Une fois allumé, le métal liquide est versé dans les moules, remplissant l’espace entre les rails. Après refroidissement, l’excès de métal est retiré et les rails sont meulés pour obtenir une finition lisse.
Références
[1] NF EN 1090-2. Exécutions des structures en acier et des structures en aluminium – Partie 2 : exigences techniques pour les structures en acier. AFNOR. Juin 2018
[2] ISO 12488-1. Appareils de levage à charge suspendue. Tolérances des galets et des voies de translation et de direction. Partie 1 : Généralités. ISO. Juillet 2012
[3] NF EN 1993-6, Eurocode 3 – Calcul des structures en acier – Partie 6 : Chemins de roulement. AFNOR. Septembre 2007.
[4] DIN 536-1, Rails pour ponts-roulants – dimensions, valeurs statiques, qualités d’acier pour rails à large patin, type A. Septembre 1991
Romain Palacios – chef de projet recherche – CTICM